Eine Kollaboration, von der Bioprinterhersteller und Anwender profitieren.
BIO INX und Puredyne arbeiten gemeinsam an einem Projekt, um der Kombination des optimalen Biomaterials mit einer präzisen Drucktechnologie noch mehr Priorität zu verleihen. Schonendes Materialhandling und präzises Dosieren steht an oberster Stelle. Deshalb hat sich BIO INX für den Druckkopf von Puredyne entschieden. Auf der diesjährigen Konferenz Termis in Manchester traf sich das Puredyne Team erstmals persönlich mit dem belgischen Biomaterialhersteller.
„Wir glauben, dass BIO INX und Puredyne eine gemeinsame Mission haben. Bei BIO INX sind wir bestrebt, dass alle unsere Materialien nach dem Prinzip ‚plug & print‘ funktionieren und somit unsere Kunden zur Optimierung des Resultats kaum selbst Hand anlegen müssen, was wiederum die Reproduzierbarkeit maximiert. Zwei Wege führen dorthin: Optimale Materialien, aber auch optimierte Geräte. Durch die Kombination der fein abgestimmten BIO INX-Materialien mit der optimierten Dosierung des Puredyne-Druckkopfes ist das schlüsselfertige Bioprinting näher denn je“, Jasper Van Hoorick, CEO von BIO INX.
Gemeinsame Versuche sind bereits vielversprechend: Bei synthetischen bis hin zu naturbelassenen Biomaterialien für extrusionsbasierte Verfahren zeigt sich, dass der Druckkopf von Puredyne und die Materialien von BIO INX ein perfektes Match bilden.
“Die Zusammenarbeit mit BIO INX bringt uns in dem Bereich der regenerativen Medizin voran und stellt die Vorteile von Puredyne in den Vordergrund. Durch die präzise Ansteuerung der Temperierungseinheit lassen sich die BIO INX-Biomaterialien optimal auf den Druckprozess einstellen und zu einem Konstrukt drucken – so können wir einen sicheren Druckprozess garantieren“, Felix Gruber, Business Development Manager Puredyne.
Forschende können sich darauf verlassen, dass das eingesetzte Biomaterial von BIO INX präzise, schonend und damit kosteneffizient dosiert wird. Dabei behalten sie die Flexibilität in der Auswahl des Bioprinters. Für die Zukunft sind bereits weitere Versuche in Planung, um Material und Druckkopf noch besser aufeinander abzustimmen.
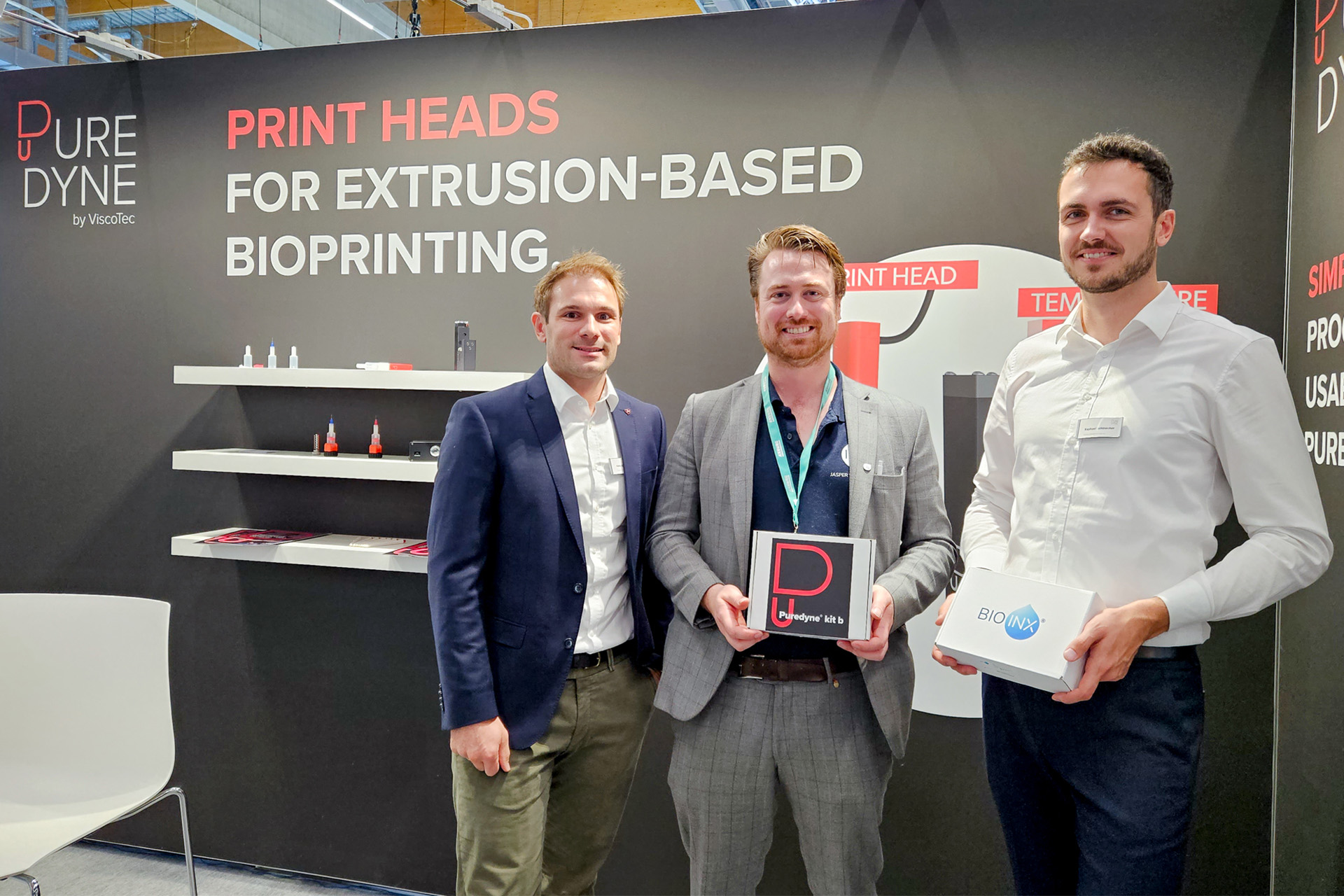
Felix Gruber, Jasper Van Hoorick und Raphael Lichtnecker (v.l.) auf der Formnext