A collaboration that benefits bioprinter manufacturers and users equally.
BIO INX and Puredyne are currently working together on a project to give even greater priority to combining the optimum biomaterial with precise printing technology. Gentle material handling and precise dispensing is the key for gaining the best results. At this year’s Termis conference in Manchester, the Puredyne team met the Belgian biomaterial manufacturer in person for the first time.
“We believe that both BIO INX and Puredyne have a shared mission. At BIO INX we strive to make all our materials ‘plug & print’, meaning that there is limited optimization needed from our customers with maximized reproducibility. There are two roads towards that: optimal materials, but also optimized equipment. With the combination of the finetuned BIO INX materials with the optimized dispensing of the Puredyne printhead, turnkey bioprinting is closer than ever.” – Jasper Van Hoorick, CEO at BIO INX.
Joint trials are already promising. From synthetic to natural biomaterials for extrusion-based processes, the Puredyne printhead and BIO INX materials are a perfect match.
“The collaboration with BIO INX brings us forward in the field of regenerative medicine and highlights the advantages of Puredyne. Thanks to the precision control of the temperature control unit, the BIO INX materials can be optimally adjusted to the printing process – so we can guarantee a safe printing process.” Felix Gruber, Business Development Manager at Puredyne.
Researchers can rely on the Puredyne printhead which doses the BIO INX biomaterial precisely, gently and therefore cost-effectively. At the same time, they retain flexibility in their choice of bioprinter. Further trials are already being planned in order to coordinate the material and print head even better.
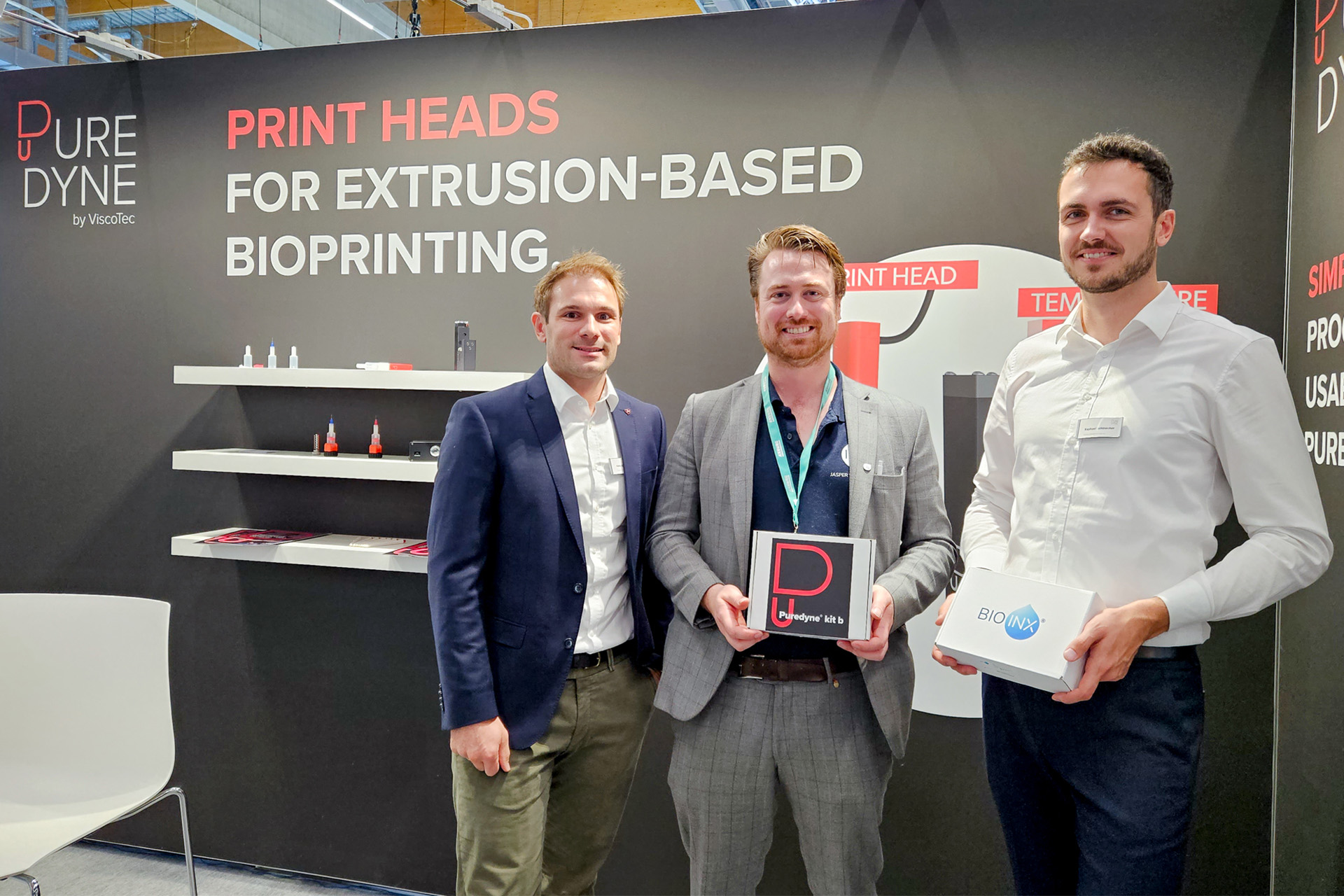
Felix Gruber, Jasper Van Hoorick and Raphael Lichtnecker (f.l.) at Formnext